- Download our full publication
- Product development deceleration has a medium-term impact on company performance
- Coordination and critical path analyses are key to fulfilling market launch dates
- The 4 main levers that can be used to optimize time-to-market in a crisis situation
- Make Project Management a science
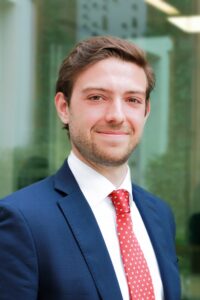

It is clear to everybody that COVID-19 is creating a terrible impact on industrial production in several sectors due to decreased consumer demand, difficulties in maintaining supply chains, and a decline in workforce efficiency. Production and sales, as well as the securitization of cash levels are critical for survival in the short term, and thus become the number one priority today.
Moreover, COVID-19 is also decelerating and in some cases completely halting fundamental activities like R&D and the introduction of new products into the market. The consequence is a strong impact visible in the medium term as a result of significant market share losses, particularly for industries where time-to-market is key – consumer goods, electronics, fashion and so on.
This article makes reference to how companies can gain competitive advantage by optimizing their time-to-market during the COVID-19 crisis.
The capability of an organization to stick to the planned market launch dates despite the crisis will provide an advantage against competitors who miss the market launch “sweet spot”. For example:
- Several consumer goods players have very short market launch slots due to seasonal consumer behavior (ex. holiday gifts, ski industry, etc.) and missing them would mean losing almost one year of sales in an already tense market situation.
- Automotive Tier 1 companies are urged by their OEM customers to secure the timely availability of their components so as to avoid jeopardizing the launch of a new model, which may create catastrophic consequences.
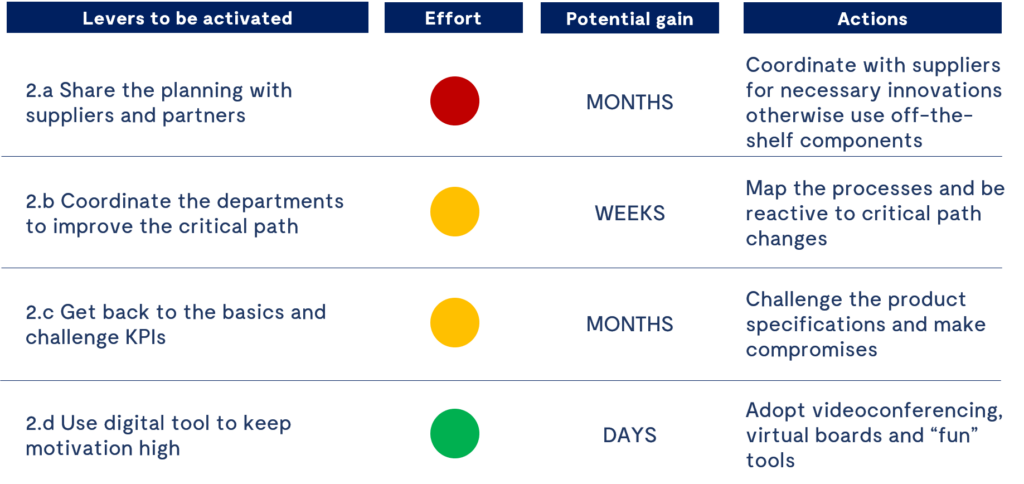
Figure 1 – 4 main levers can be used to optimize time-to-market in a crisis situation. Their impact can range from days to months of planning reduction time.
In recent projects with our clients, we have activated 4 main levers to secure or even boost time-to-market in these exceptional circumstances:
Share the planning with suppliers and partners
Innovative products use innovative components by suppliers, often still in their development phases and not yet present in the catalogue. Due to specific national policies or management decisions to handle the crisis, the development planning of suppliers and other partners could experience different drifting. This results in planning desynchronization due to strong external constraints, which becomes a difficult task for project managers to solve.
To recover from this situation, project managers needs to take some countermeasures:
- Carry out an adapted project risk analysis to identify and prioritize all of the perturbing factors introduced by the crisis
- Strengthen their collaboration with key partners and suppliers to re-align all of the development activities, especially for the components which are key to final product performance
- Revert to components already in the market when innovation is not necessary or impossible at that stage
Coordinate the departments to improve the critical path
As the COVID-19 crisis impacts every company’s department in a different way, delays increase in an uneven manner, strongly affecting the critical path of the project. For instance, testing activities could be slowed down significantly and thus become critical, and R&D engineers could not progress due to the lack of inputs.
Project managers need to deploy a methodology to quickly identify the modifications in the critical path and reprioritize development activities in order to recover the initial due date. This can be done via advanced functions in project management tools, such as MS Project, which allow sensitivity measurement of the critical path as a result of the drifting of specific activities.
As a caveat, note that oftentimes it will be difficult to completely fill the resource workload availability in the revised planning: a match between project needs and other possible activities (ex: trainings) must be conducted with the support of HR and managers.
Get back to the basics and challenge KPIs
The objectives of a project are usually a balance between new product specifications fulfilment, market launch due date, and meeting target costs. In order to reduce the duration of the planning, a flexible compromise may become necessary on specifications and costs.
Among the available options for project managers, we may suggest to:
- Challenge the benefits (customer value) vs effort (R&D development and test campaign) of the product specifications in order to re-focus engineers and laboratory technicians on the key requirements
- Compromise on, or postpone in a 2nd phase, possible cost-reduction or operational improvements in exchange for reducing development time
- Challenge the time-to-market objective with the marketing department to assess if any constraints can be relaxed (ex: impact of postponing the launch, or launching a designated portion of the product range, etc).
Use digital tools to keep motivation high
R&D is one of the departments where the ability to work from home has been most widely adopted, due to the ability to perform many activities remotely. However, these working conditions are far from optimal for many engineers lacking the access to their standard tools and working arrangements, and may be even further compounded for sub-contractors who could not have made time to be integrated in the team before the crisis.
Project managers should dispose of and rely on modern digital tools to manage the project and communicate its progress: this will have a positive impact on team morale. Main tools include:
- Videoconference tools like MS-Teams, Zoom, Skype
- Virtual boards (such as iObeya) where team members can note the topics they are working on and ask questions about the workflow of their colleagues
- “Fun” platforms to gather ideas and opinions (such as Foxtwin) depending on the willingness of the team
In order to implement the practices described here, personal intuition is not enough to face today’s complexity: project managers need to take advantage of modern digital tools to search for optimization levers.
Process mapping (MS Visio)
Process mapping is a graphic method to clarify the links among tasks and to streamline planning. Development tasks are identified, quantified (duration, workload, resources) and structured in order to show the input/output relationships with other tasks and external entities, such as other departments or suppliers. I found that MS Visio functions well for quickly creating and modifying visual charts during workshops with the team.
Project management software (MS Project)
Project management software allows the project manager to identify critical and sub-critical paths, have a clear understanding of the impact of a delay in some activities on the overall planning, and to control resource workload. I usually start from a Process Map and translate it into MS Project, where I perform empirical and mathematical optimization via the levelling functions. Afterwards, it becomes easy to validate the planning feasibility via the resource utilization graphs.
Digital PMO platforms (iObeya)
Digital PMO platforms are useful to manage the project on a daily/weekly basis and they can be a substitute for whiteboards and post-its. Theses digital platforms are particularly suited for the current circumstances because they are SaaS and can be accessed and modified by all users independently. I use iObeya to animate weekly meetings and then insert the task progression into MS Project to compute the impact on the overall planning.
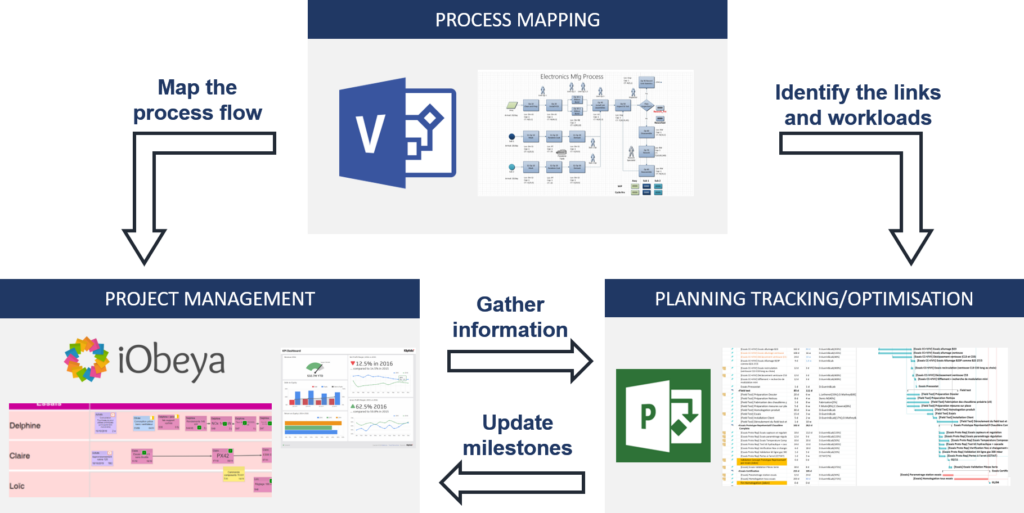
Figure 2: Standard flow of information among project management tools
Tangible results at each mission
July 17, 2023
The space industry’s path to a sustainable future
July 4, 2023
Measure R&D performance
June 19, 2023
Standardization perspectives of nuclear plants
June 8, 2023